MOTEK Crusher Buckets in Quarrying
Release time: 2025-04-22
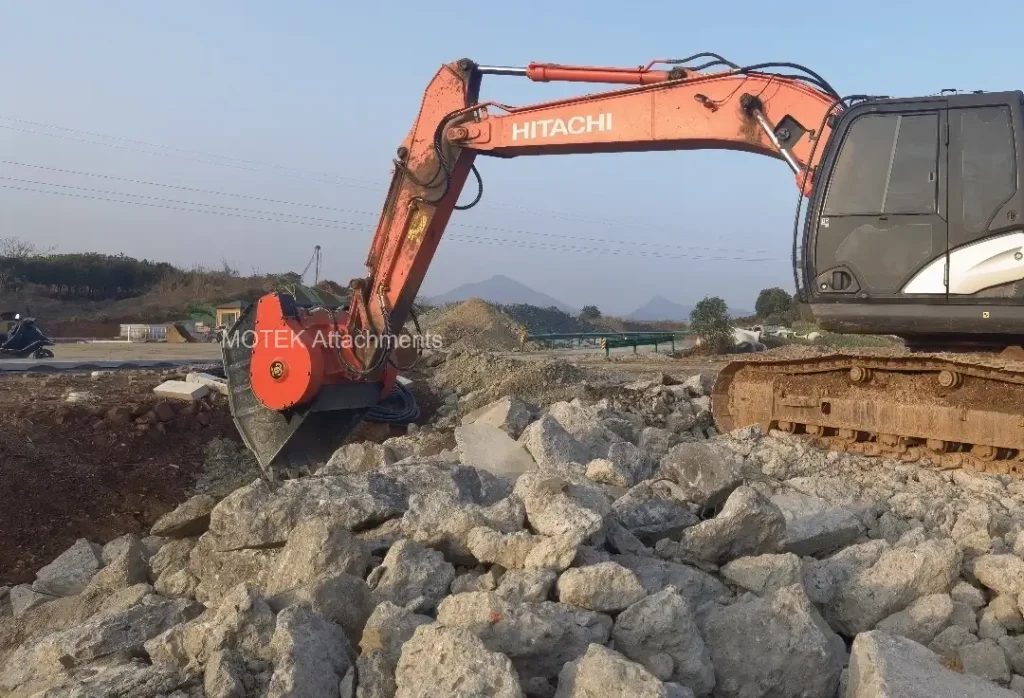
As a raw material supply base for infrastructure construction such as buildings and roads, the operating efficiency and cost control of quarries directly affect the progress of projects and economic benefits. In traditional quarrying operations, the mining, crushing, and transportation of stone materials require multiple devices and complex processes. Crusher buckets, as an efficient and flexible engineering machinery accessory, have gradually become an innovative tool for quarrying operations in recent years.
The role of the crushing bucket in the quarry
Direct on-site crushing to simplify the production process: Traditional quarries need to use blasting or large crushers to initially crush large pieces of raw stone, and then use transportation equipment to send the stone to a fixed crushing station for secondary processing. MOTEK crusher bucket is directly installed on the excavator, which can crush large pieces of rock immediately at the mining site, eliminating the intermediate transportation link and realizing the integrated operation of “mining-crushing-loading”. This on-site processing method greatly shortens the production chain and reduces time and labor costs.
Flexible adjustment of crushing size to meet diverse needs: MOTEK excavator crusher bucket can control the output size (usually 20-200 mm) by adjusting hydraulic parameters or replacing jaw plates of different specifications. The quarry can flexibly adjust the crushed stone size according to downstream needs (such as roadbed filling, concrete aggregate, etc.), reduce the workload of subsequent screening links, and improve the adaptability of finished stone.
Handling complex working conditions and improving resource utilization: Quarries often encounter irregular rocks, impure rock layers or leftovers, which are difficult to handle efficiently with traditional equipment. With its powerful hydraulic drive and wear-resistant design, the crushing bucket can crush rocks with a hardness of up to 250MPa and separate soil and stones, thereby improving the utilization rate of low-grade ores and reducing resource waste.
Reduce reliance on blasting and reduce safety risks: Traditional blasting methods have safety hazards such as flying rocks, vibration, and dust pollution, and require strict approval procedures. MOTEK crusher bucket attachment breaks rocks through mechanical force without the use of explosives, significantly reducing safety risks and reducing interference with the surrounding environment. It is especially suitable for quarries near residential areas or ecologically sensitive areas.
Significant cost-effectiveness
– Low equipment investment: As an excavator attachment, MOTEK concrete crusher bucket does not need to purchase large crushing equipment separately. It can be quickly deployed using existing excavators, saving millions of fixed investments.
– Low operating costs: It saves blasting costs, energy consumption and maintenance costs of transport vehicles and fixed crushing stations. Taking a medium-sized quarry as an example, the use of a crusher bucket can reduce the overall cost by about 30%-40%.
– Labor cost optimization: Integrated operation reduces the number of equipment operators and reduces the scheduling and management costs caused by complex processes.
Significantly improved operating efficiency
– Shortened production cycle: In-situ crushing reduces stone transportation time, and its efficiency far exceeds the traditional multi-link operation mode.
– Strong continuous operation capability: MOTEK digger crusher bucketdoes not need to change the operating position frequently, and supports long-term continuous crushing, which is especially suitable for large-scale mining of high-hardness rocks.
– Quick switching function: The same excavator can quickly replace MOTEK rock crusher excavator bucket and other accessories (such as buckets, hydraulic clamps), adapting to the multi-task requirements of the quarry and improving equipment utilization
Outstanding environmental protection and safety
– Reduce pollution emissions: avoid dust, noise and vibration caused by blasting, in line with the requirements of green mine construction.
– Reduce accident risks: mechanical crushing replaces manual blasting, eliminates potential dangers in the storage and use of explosives, and reduces collision accidents caused by heavy transport vehicles in the field.
– Eco-friendliness: precise crushing reduces structural damage to surrounding rock formations, which is conducive to ecological restoration of the quarry and maintenance of slope stability
Adapt to complex terrain and flexible deployment
– Strong terrain compatibility: MOTEK crusher bucket is mounted on the excavator and can penetrate into steep slopes, narrow pits and other areas that are difficult for large equipment to reach, expanding the mining range of the quarry.
– High mobility: No fixed infrastructure is required, and the operation point can be quickly transferred as the quarrying progresses, which is especially suitable for decentralized mines or small quarries.
– Emergency handling capabilities: In the event of sudden landslides or large rock blockages, the crushing bucket can be quickly called for on-site cleaning to reduce downtime.
MOTEK crusher bucket is reshaping the traditional operation mode of quarries with its high efficiency, flexibility and environmental protection. It not only simplifies the production process and reduces the overall cost through “in-situ crushing”, but also meets the needs of modern mines for green and flexibility with excellent safety and adaptability. With the iteration of technology and policy promotion, MOTEK hydraulic crusher bucket will become one of the core equipment for improving the quality and efficiency of quarries, helping the industry to transform towards intensive and sustainable directions. For quarry operators, the introduction of crushing buckets is not only a choice for technological upgrading, but also a strategic investment to enhance market competitiveness.